Why dry?
Drying is the process of removing liquid from solids by evaporation. The drying process has been used for thousands of years to reduce transport weight and increase the storage life of numerous products and materials. For centuries, drying meant spreading a product out in the open air and letting the sun provide the energy for water evaporation. With the dawn of the industrial age, many different drying processes have been developed to increase drying speed and improve product quality and uniformity.
Why Spray Dry?
In the world of industrial dryers, there are few types that accept pumpable fluids as the feed material at the inlet end of the process and produce dry particulate at the outlet. Spray drying is unique in its ability to produce powders with a specific particle size and moisture content without regard for the capacity of the dryer and the heat sensitivity of the product. This flexibility makes spray drying the process of choice for many industrial drying operations.
Advantages of spray drying:
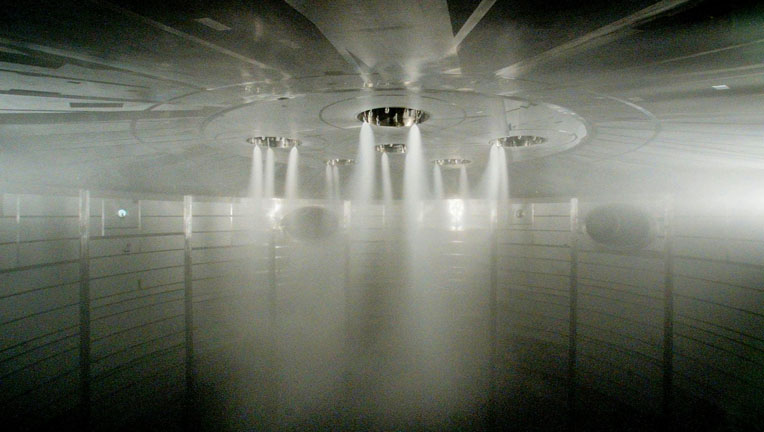
- Able to operate in applications that range from aseptic pharmaceutical processing to ceramic powder production.
- Can be designed to virtually any capacity required. Feed rates range from a few pounds per hour to over 50 tons per hour.
- Powder quality remains constant during the entire run of the dryer.
- Operation is continuous and adaptable to full automatic control.
- A great variety of spray dryer designs are available to meet various product specifications.
- Can be used with both heat-resistant and heat sensitive products.
- As long as they are can be pumped, the feedstock can be abrasive, corrosive, flammable, explosive or toxic.
- Feedstock can be in solution, slurry, paste, gel, suspension or melt form.
- Product density can be controlled
- Nearly spherical particles can be produced.
- Material does not contact metal surfaces until dried, reducing corrosion problems.
Brief history of spray drying
Late 1800s
The development of spray drying equipment and techniques evolved over a period of several decades from the 1870s through the early 1900s. The first known spray dryers used nozzle atomizers, with rotary atomizers introduced several decades later. Because of the relatively unsophisticated designs of the early spray dryers and practical difficulties in operating them continuously, very little commercial use of the process was made until the 1920s.
20th century
By the second decade of the twentieth century, the evolution of spray dryer design made commercial operations practical. Milk drying was the first major commercial application of the technology. During the next 20 years, manufacturers developed designs to accommodate heat-sensitive products, emulsions and mixtures. Spray drying came of age during World War II, with the sudden need to reduce the transport weight of foods and other materials. This surge in interest led to developments in the technology that greatly expanded the range of products that could be successfully spray dried.